
Engineering Design Portfolio
Zijian Wang (James)
Mechanical Engineering UofT
Machining and Construction: Pneumatic Engine

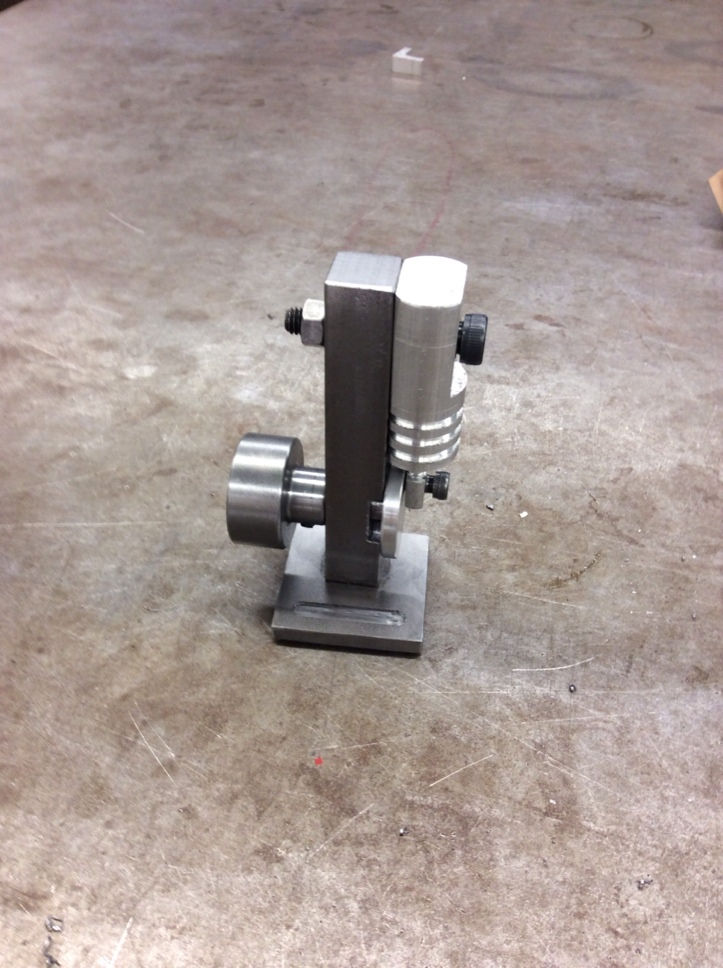
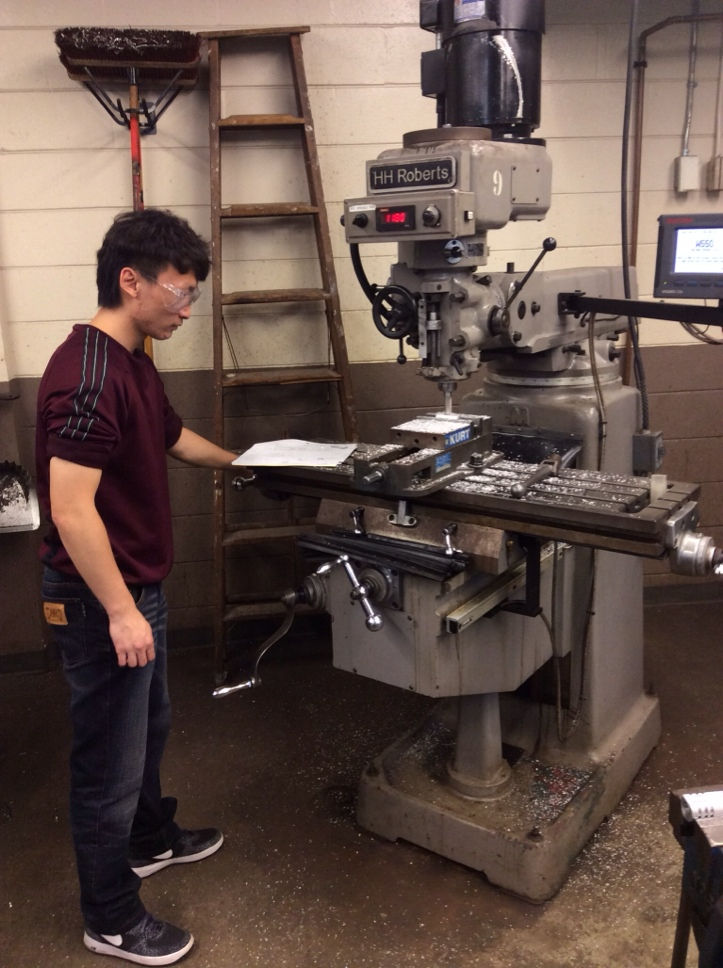

This task of assembly of machined parts for a pneumatic engine, which was completed in George Brown College, has demonstrated my precise machining skills and strengthened my measuring skills of using common measuring equipment.
To accomplish the task, it requires the candidate to proficiently use lathe, mill and tapper in a machine shop. The priority of the task is to comprehensively understand what the technical drawings mean, so that further actions can be taken. To approach to the final product as laying out in the drawings, precise and accurate measurements need to be applied first. My skill of using measuring tools such as non-digital caliper and micrometer has been improved to most extent. By following measuring process, proficiency in setup and maneuvering lathe and mill is a necessity.
After finishing machining each component of the pneumatic engine, the task asked each candidate to assemble all the components into a moving engine mechanism, which was tested under a simulating pressure condition. Before the test, my piston always got stuck in the cylinder. Afterwards, by dissembling all the components and applying motion analysis separately on each part, I found out that the major cause of frequent jam of the piston was an extruding screw through a misaligned tapper on the drive shaft wheel, which led to high friction between the main supports. By fining this flaw, I realize how important accuracy is in machining. One single misaligning issue will cause the entire engine to jam. However, what’s more important to an engineering designer is to analyze the problem, never give up and eventually find cause(s) and solution(s) to the problem.
The machining experience in George Brown College provided me with some insights as engineering designers, of which we should design components for manufacturability and easy machinability.